

Sami Mattila placing 3D printed items in automatic blasting machine to remove powder residue “We developed this technique to be able to start a new print session immediately instead of letting the machine cool down,” explained Sami Mattila, one of the co-founders of Materflow. As an example of what Hassett said, the original patent for SLS 3D printing expired in 2014, and technicians at Materflow developed a technique where the block of powder containing the 3D printed objects is removed from the 177☌ printer interior and placed inside a sealed wooden box for 24 hours, or until the temperature drops to 60☌. The OMEDELBAR hand is 3D printed at Materflow in Finland, using the powder-based Selective Laser Sintering (SLS) process, and post-processed at Germany’s DyeMansion. “At the same time, a couple of vital patents have expired in the last few years, making it possible for the industry to start producing cheaper materials, more advanced machines and allowing us to create a purpose-built supply chain to make 3D mass production accessible.”
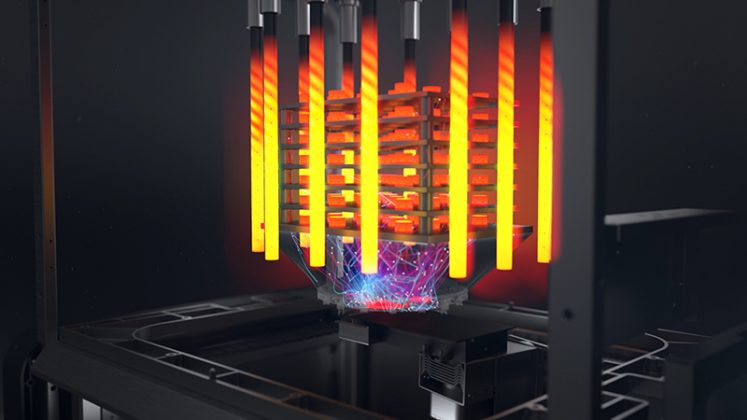
Big players are releasing new techniques of their own,” said Hassett. Hassett certainly knows what he’s talking about – Ireland-based Wazp, which is collaborating with IKEA on the OMEDELBAR collection, is a pioneer in 3D printing for mass production, and the company is one of the world’s biggest manufacturers, by volume, of 3D printed objects.
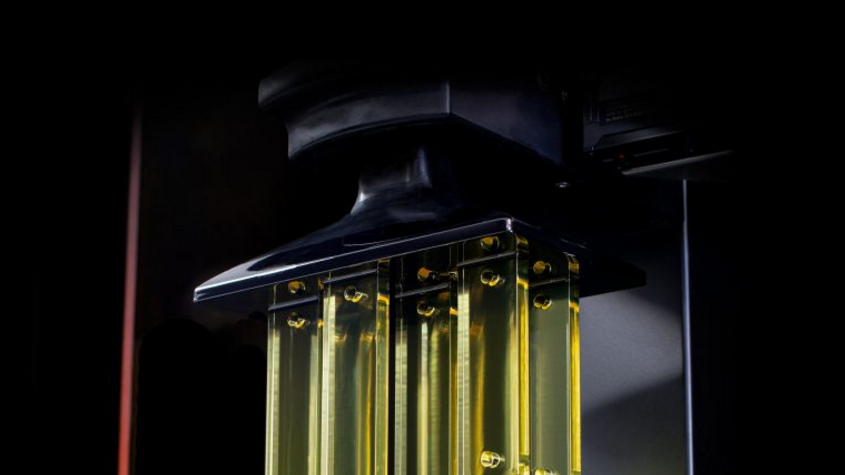
As Shane Hassett, the CEO of Wazp, puts it, the industry of mass produced items has long been controlled by the inventors who filed patents for their methods and techniques – but this is starting to change, and 3D printing in mass production is becoming more accepted. As with many other 3D printed products, the complex design of the OMEDELBAR hand would not be possible without 3D printing technology – conventional methods, like injection molding, are too expensive.ģD printed systems for mass production are not unheard of – last year, Hyproline’s PrintValley system became the first high-speed, metal 3D printing system for post-processing, verification, and mass production, and Tamicare’s 3D textile printing technology went into mass production in 2015. The 3D printed hand looks like it’s reaching out for something, and can be used as a decorative jewelry holder or a piece of unique wall art. The OMEDELBAR collection features a mesh-inspired design of a stylistic, deconstructed human hand. In that context, the OMEDELBAR hand will have its place in design production history.” Now, we are closing fast on the breaking point where 3D is cost efficient in mass production. Traditionally the technology has been used for prototyping in high-tech industries or moulds used for traditional production methods. “We started this project one and a half years ago, predicting the boom in 3D printing in mass production. It demonstrates how IKEA, being an innovative company, is always on the search for new ways of doing things and explore the latest technology to do so. “As one of the first major brands, IKEA will be using 3D printing in furnishing mass production,” said Pawlak.
#MASS PRODUCTION 3D PRINTING FREE#
Jakub Pawlak, with Trader Free Range IKEA Poland, is in charge of the groundbreaking project. IKEA announced that it will be releasing the unique OMEDELBAR collection next year, in collaboration with stylist Bea Åkerlund. But now, IKEA is introducing its first mass produced 3D printed home objects. However, the collection, which features experimental designs, is only periodic. 3D printing technology is being used more often in furnishings and home decor, and IKEA itself even featured a 3D knitted chair in its PS 2017 collection.

But I usually risk it anyway, because I really enjoy the experience of walking through that massive store maze, surrounded by beautifully furnished room setups and checking out all of the random clearance items at the end. I’m always a little wary about going to IKEA, because I know I’ll end up buying something I absolutely do not need.
